January 24, 2020 Guest opinion piece
In my book, “Recipe for success – the ingredients of a profitable food company”, I have a whole chapter on the “F*** up fairy” who basically comes along and takes away all that profit that you have so carefully made through the previous 11 chapters. Below are two examples of how I have personally experienced her work and how it has cost my clients thousands of lost profits.
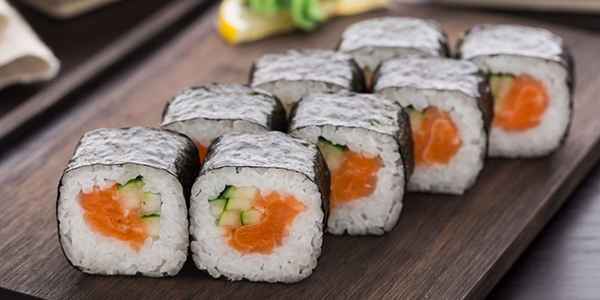
Case study 1: Metal contamination
In a past life, I worked for a sushi company. They were meticulous in their Hazard Analysis and Critical Control Point (HACCP) and control procedures, and yet they suffered a metal contamination that cost them nearly £500k (when you took into account lost sales, loss of profit compensation and the write-off of contaminated stock).
The problem we quickly discovered was in the rice. It had not been metal checked by our supplier and found its way onto our line, where our own safety procedures picked it up, but not before we had sent out product (we later discovered other companies who used that rice, in not just sushi, had the same issue).
We stopped production, told the retail customers and switched rice supply. We had sushi back on the shelf within 48 hours, but the cost was widespread. Some of the costs included:
- Wasted product stock
- Wasted raw materials
- Charges by retailers – loss of profit, wasted stock
- Lost sales by being off shelf
- Investment in time getting the new products back on the shelf
As a business we did have insurance for this type of event which covered some of the losses (about a third). It is virtually impossible to get insurance to cover retailer loss of profit, as it is an open cheque book.
The manufacturer did try to claim from the supplier – but negotiations were still ongoing a year later!
Fortunately in this case, the reputation of the sushi company was maintained due to the swift way we dealt with the problem – sometimes, it is the handling of a crisis which gains you more respect than the respect you lost from the crisis in the first place!
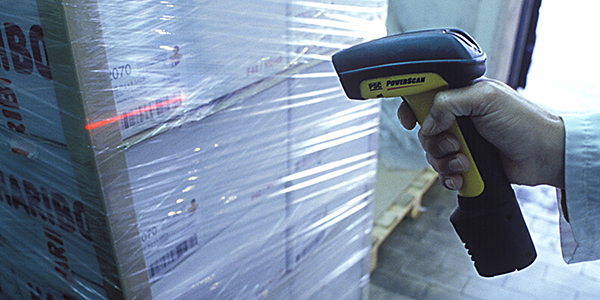
Case study 2: The cost of the barcode that didn’t read!
Barcodes may appear to be little more than an administrative part of the very long and complex business of launching new products. There are systems in place to make sure you have the right ones on the right products and often conscientious companies will go into store to make sure the barcode is scanning correctly at the right price, on the right product.
But what about outer case barcodes?
I was working with a client who decided to save money by having one standard outer case and would print the barcode and product information onto each one. It was a system that worked well and there had been no issues. They then changed the printer, didn’t check if the barcodes were scanning correctly and off the products went. We heard nothing from the retailer, sales were normal…. all good, or so we thought!
A week later, I had an email to say that the outer case barcodes were not scanning and had not been for nearly a week. Clearly the warehouses had not been stopping the products going through as we were still selling product. So, we apologised and changed the printer to improve the quality of the barcode and all should have been well: apart from the small charge of £500 for a wrong barcode.
However, because it was four days before the retailer got in contact - not their fault, we had not updated our contact details - and we had nearly 40 products, we ended up with a potential fine in excess of £60,000… all because of a barcode that doesn’t scan.
The moral of this story: make sure you check that the barcodes scan on both inner and outer packaging, read the small print of your retailer agreements and make sure they can get in touch immediately if there is an issue!!
Be confident in you barcode images
To avoid potential fines from barcodes not scanning correctly, GS1 UK - the company that licenses all the barcode numbers in the UK - offer a service to review your barcode images and ensure they meet the latest global standards. The team make sure:
- The Global Trade Item Number (GTIN) or Serial Shipping Container Code (SSCC) is in the correct format
- The barcode is correctly sized and positioned
- Appropriate colours are used
- Your label design allows for accurate scanning
They then offer a report outlining and recommended improvements, along with support for whatever you need to do.
To find out more about this service and to be confident in what you are sharing with your customers, just click the button below.